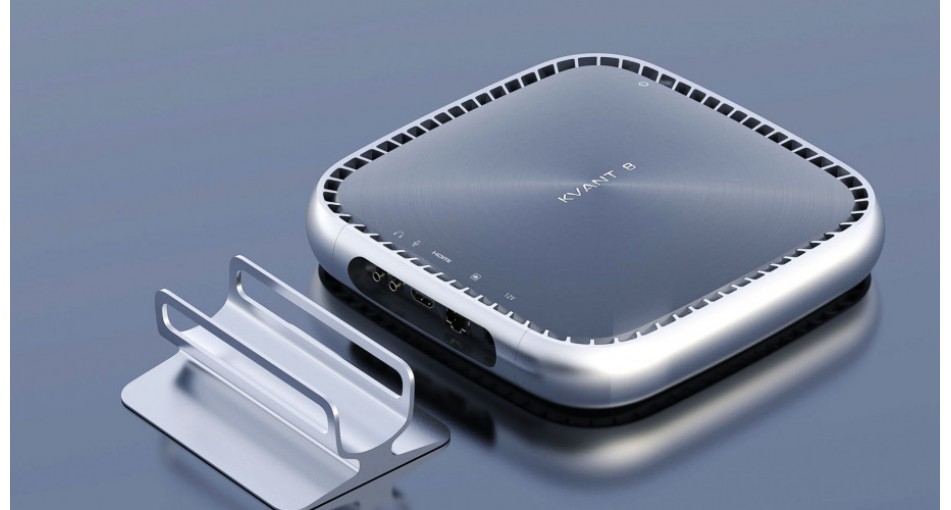
При разработке и производстве корпусов пластмасса — едва ли не первый вариант, который рассматривают разработчики. Это универсальный материал: за счет тысяч вариантов полимеров можно создать пластмассу со нужными механическими свойствами. Мы собрали 8 самых популярных способов производства продуктов из пластмасс. Будет полезно как инженеру, так и промышленному дизайнеру.
Выбор метода производства пластикового корпуса
Выбирая конкретный метод для производства пластикового корпуса прибора или устройства, принимайте во внимание:
- форму корпуса;
- его тираж и себестоимость;
- сроки производства изделия;
- условия эксплуатации корпуса.
Форма
Простая форма у вашего корпуса или сложная? Нужны ли жесткие допуски?
Если с простой все понятно, то для сложной с выборами технологии производства пластикового корпуса разбегаться некуда. Геометрия изделия будет диктовать технологию (или будьте готовы к серьезным конструкторским доработкам).
Тираж и себестоимость
Определились, сколько единиц продукта вы будете производить в ближайший год и далее? Это важно: в одном случае у вас будут большие начальные затраты (изготовление пресс-форм, например), зато стоимость производства пластикового корпуса окажется невысокой. В других случаях — приемлемые цены на первом этапе, но «средняя» стоимость за единицу корпуса, которая не будет снижаться с ростом тиража.
Сроки производства
На том же 3D-принтере можно и за сутки что-то напечатать. А почти все другие способы — это часто месяцы подготовки.
Условия эксплуатации корпуса
Оцените требования к продукту и исходя из них подбирайте материал. Должен ли ваш прибор быть антивандальным? Выдерживать падение с двухметровой высоты? Допускаете ли вы, что со временем его цвет поблекнет (или пожелтеет), будет выгорать на солнце? Исходя из требований и делайте выбор.
Виды пластмасс
Их тысячи. Они отличаются друг от друга химсоставом, добавками и производным. Два основных вида (по частоте использования в производстве): термопластики и термореактивные пластмассы.
Термопластики (термопласты)
Самые популярные пластмассы. При высокой температуре термопластики становятся гибкими и вязкими, при охлаждении затвердевают. Их легко можно «переплавлять» несколько раз без потери качества, потеря свойств здесь некритична. Форма — гранулы или листы, которые можно формовать. Это тот материал, который можно перерабатывать. Среди термопластиков известны акрил (ПММА), акрилонитрил-бутадиен-стирол (АБС), полиамид (ПA), полимолочная кислота (ПЛА), поликарбонат (ПК), полиэфирэфиркетон (ПЭЭК), полиэтилен (ПЭ), полипропилен (ПП), поливинилхлорид (ПВХ).
Термореактивные пластмассы (термореактивные материалы)
В отличие от термопластиков, термореактивные пластмассы переработать нельзя. При химической реакции образуется трехмерная структура, которую потом невозможно расплавить: процесс необратим. Самые известные виды таких пластмасс — цианатный эфир, эпоксидная смола, полиэфир, полиуретан, силикон, вулканизированная резина.
Методы производства корпусов из пластмасс
- Литье:
- под давлением;
- центробежное (или ротационное);
- литье полимеров. - Обработка на станке с ЧПУ.
- Экструзия.
- Формовка:
- вакуумная;
- выдувная. - 3D-печать.
Литье под давлением
Самый распространенный метод для массового производства пластиковых корпусов, при котором расплавленный термопластик впрыскивают в пресс-форму.
Как все происходит: сначала проводится настройка пресс-формы (вставки в форму добавляют отдельно, после чего ее закрывают); пластиковые гранулы материала расплавляют и экструдируют через нагретую камеру с помощью шнека. Следующий этап — формование, когда горячий пластик впрыскивается в пресс-форму. Дожидаются, пока пластик в пресс-форме не охладится, извлекают полученное изделие из формы. Постобработка (очистка от литников и/или заусенцев) проходит иногда автоматически – в тот момент, когда изделие покидает пресс-форму, а иногда литники отламывает и обрезает человек.
Пресс-форма — точная, сложная инженерная конструкция и дорогое удовольствие. Процесс проектирования пресс-формы может занять несколько месяцев. Они бывают стальными и алюминиевыми. Алюминиевая форма быстрее деградирует в процессе литья. Кроме того, в такой форме не получается хорошо реализовать подвижные элементы. Как следствие, в алюминиевых формах можно отливать только простые детали.
Плюсы при производстве пластиковых корпусов — высокая точность изготовления, производство даже миллионных тиражей (минимальный — 500 единиц), небольшие сроки изготовления (два-три месяца), материалы — любой термопластик.
Минусы — большие вложения на начальном этапе и достаточно долгие сроки запуска производства.
Материал для производства: для литья под давлением можно использовать практически любой тип термопластика. Подробности — в статье «Материалы для литья под давлением».
Мы используем литье под давлением для разработки и производства таких пластиковых корпусов:
Литье полимеров в силиконовые формы
Полимеры относятся к термореактивным пластмассам. В процессе производства пластикового корпуса реактивный жидкий полимер смешивается с отвердителем и постепенно затвердевает.
Как все происходит: подготавливается пресс-форма (ее покрывают особым составом для быстрого извлечения заготовки), полимер смешивают с отвердителем, дегазируют в вакууме, чтобы удалить пузырьки воздуха, и льют в форму. Материал полимеризуется и твердеет. После извлечения пластиковой детали литники и заусенцы обрезаются, швы шлифуются.
Плюсы: Пресс-формы из силикона недороги — это позволяет сэкономить на старте производства. Можно достичь высокого качества литья, с мелкими деталями. Да и проектировать такие детали относительно просто: можно закрыть глаза на уклоны, разнотолщинность. Срок изготовления — от суток до недели.
Минусы: одна силиконовая форма выдерживает от 20 до 40 отливок, больших тиражей здесь вы не получите. Максимальной эффективности можно достичь при тираже до 1000 шт. Есть ограничения, свойственные этой технологии: например, очень тонкие стенки, тоньше 2 мм, могут не «пролиться».
Ну и ручная постобработка: человеческий труд всегда дороже машинного.
Материалы для производства. Для литья обычно используют полиуретан, акрил, эпоксидную смолу и силикон.
Мы используем литье полимеров для таких корпусов:
Центробежное литье (ротационное формование)
Используется для производства полых пластиковых корпусов. Полая пресс-форма заполняется порошкообразным термопластом и вращается вокруг двух осей.
Как все происходит: форма заполняется пластиковым порошком, в нее устанавливают оставшиеся части формы (или отдельные элементы, такие как внутренние трубы или металлическая резьба), а затем закрывают. После чего нагревают, пока порошок не начнет плавиться. Одновременно пресс-форма особым образом вращается, что позволяет материалу ровно распределиться. Чтобы корпус не деформировался, охлаждение также происходит одновременно с вращением. После извлечения из формы с продукта убирают заусенцы.
Формы делаются из алюминия или эпоксидной смолы. Плюсы здесь: относительно быстро и недорого. Метод производства хорош для мелких серий, сроки изготовления изделий — также небольшие, от пары дней до пары недель.
Минусы: для больших тиражей этот способ невыгоден из-за трудоемкости, продукт с жесткими допусками этим способом не получить. Максимальный тираж здесь — 5000 единиц.
Материал для производства — как правило, полиэтилен. Метод подходит и для термореактивных пластиков, но используется нечасто.
Обработка на станках с ЧПУ
Это, как правило, фрезерные и токарные станки. «Лишний» материал из пластиковой заготовки удаляется давильными инструментами/ фиксированными инструментами/деталями — сверлением, резкой, растачиванием и шлифованием.
Как все происходит: производится настройка станков в плане настройки траекторий движения режущих инструментов, затем на станке начинается непосредственно обработка. После того, как все высверлено, вырезано, отточено и отшлифовано, деталь либо переворачивают, чтобы инструменты смогли добраться до тех участков, до которых не дошли на первом этапе, либо, если все сделано, отправляют на постобработку, где очищают от заусенцев и обрезают.
Плюсы: метод оптимален для производства пластиковых корпусов с жесткими допусками, а также прототипирования. Сроки изготовления деталей — короткие от суток, стоимость корпусов — приемлемая.
Минусы: необходима постобработка — покраска, например. Стоимость производства пластикового корпуса увеличивается соответветственно сложности, есть ряд ограничений по геометрии корпуса. Подходит для тиражей до 5000 единиц.
Материалы: можно использовать как термореактивные пластмассы, так и термопластики — с учетом особенностей каждого типа.
Мы используем обработку для таких корпусов:
Пластиковая экструзия
Пластик продавливается через формующее отверстие, которое представляет собой поперечное сечение детали.
Как все происходит: нагретый пластик шнеком продавливается через нагретую камеру, затем попадает в формующее отверстие (фильеру). Затем пластик охлаждают, полученную заготовку либо режут, либо наматывают на катушку.
Плюсы: низкая стоимость конечных изделий.
Минусы: с помощью пластиковой экструзии можно получить относительно простые и не высокоточные формы. Сроки изготовления: средние, тиражи — от средних (1000 единиц) до крупных.
Материалом для производства пластиковых корпусов может служить почти любой термопластик.
Вакуумная формовка
Пластик нагревают и с помощью формы (удивительно!) формуют.
Как все происходит: пластиковая заготовка в виде листа зажимается в раме, пластиковый лист нагревают, затем раму опускают. Пластик обтягивает пресс-форму. Одновременно с помощью вакуума из пространства между пластиком и формой откачивается воздух. Деталь охлаждают, снимают с формы, излишки убирают вручную или с помощью станков.
Формы для вакуумной формовки недороги, поскольку изготавливаются из дерева, гипса или даже пластмассы. Для больших тиражей потребуются металлические формы.
Плюсы: быстрое изготовление, от суток, любые объемы производства.
Минусы — ограничения по формам, толщине стенок и геометрии. При формовке детали из листа его толщина уменьшается и может быть неоднородной по площади детали. Где сильнее вытянуто — там тоньше.
В качестве материала для вакуумной формовки подходят термопластики.
Мы используем вакуумную формовку для проектов, похожих на этот:
Выдувная формовка
Подходит для производства полых пластиковых корпусов. Внутрь формы помещается пластиковая трубка и нагревается в ней до тех пор, пока не примет нужную форму.
Как все происходит: сначала из пластиковых гранул формируется полая трубка, потом ее помещают в пресс-форму. Под воздействием сжатого воздуха нагретый пластик прижимается к стенкам формы. После чего деталь охлаждают.
Выдувное формование требует гораздо более низких показателей давления, чем литье под давлением, а инструментарий для него стоит дешевле. Подобно литью под давлением и экструзии, выдувное формование — непрерывный процесс, который можно полностью автоматизировать, что обеспечивает высокую производительность и низкие затраты на единицу продукции.
Плюсы: низкая стоимость деталей, подходит для крупных тиражей (свыше 5000 единиц).
Минус: произвести можно полые детали с несложной геометрией. Сроки изготовления — средние: несколько недель.
В качестве материалов подходят термопластики.
3D-печать
3D-принтеры печатают послойно, что позволяет напечатать продукт практически любой формы. Файл для печати можно загрузить прямо из программы автоматического проектирования. Это:
а) экономит время;
б) недорого (но при единичной печати или при производстве мелких партий корпусов, до 1000 штук).
Как все происходит: настраивается ПО для печати, затем запускается сам процесс печати выбранным методом (FDM — наплавление; SLA — стереолитография, SLS — расплавление порошка; подробнее читайте в этой статье), а после изделие уходит на постобработку (это очищение и промывка, а также финальная полимеризация).
Плюсы: быстро, недорого.
Минусы: требует постобработки поверхности. Большие тиражи печатать невыгодно — раз, все будет долго — два. И качество у таких хотя и все «более лучше», изделий пока не на высшем уровне.
Поэтому делать ставку 3D-печать в качестве серийного производства корпусов мы не рекомендуем.
Материалы: при 3D-печати используются термопластики.
Мы используем 3D-печать в основном для макетов, редко — прототипов. Почему, читайте статью «Когда 3D-печать бесполезна и почему» или смотрите видео.
А о том, как выбрать правильную технологию для прототипирования корпуса, читайте здесь. Об отличиях макета от прототипа — здесь.